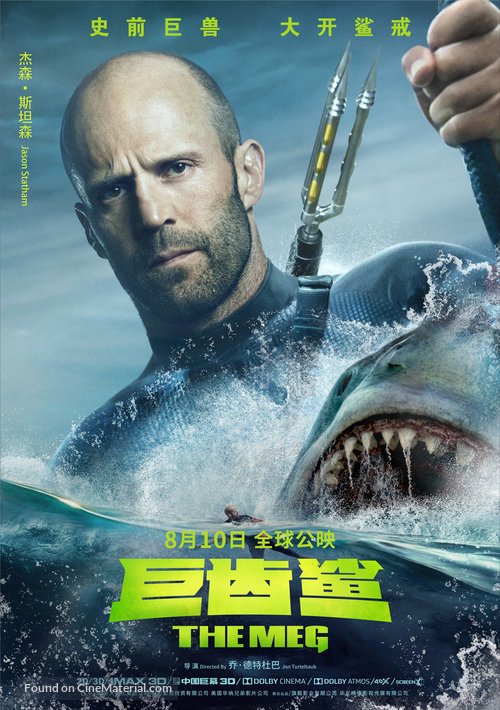
It's unitizing---assembling products into a single unit--usually on a pallet---that makes packaging and shipping both efficient and cost-effective. Unitizing products reduces handling costs and saves time. It ensures a safer, more efficient distribution process, while protecting products from damage and theft. Applying stretch film is one of the most common and most secure methods of accomplishing this.
The goal for choosing the best stretch film is to find one that fits your company's specific need without paying for unneeded properties. For example, loads that will spend most of their days in a warehouse or shipping container, don't need film with UV light protection. On the other hand, loads with lightweight film that don't fit snugly to the pallet corners are subject to punctured film and shifting loads. But if you've never used stretch film before or aren't happy with the film you're using, how do you know which one is right? Following are 6 considerations for choosing the best stretch film for the job.
Primary Cost Comparisons: Price/lb. vs. Price/ft. vs. Price/load
When talking to a stretch film salesperson, trying to figure out how their product compares to the product the consumer is currently using can be confusing. All film is sold by the pound. Traditional films that typically have higher gauges are actually less expensive per pound because they use less expensive plastic resins to make the film. The high performance films are more expensive because they are manufactured with better quality resins and can be layered. This is a more expensive manufacturing process. The high performance films generally end up costing less overall because the film's light weight offsets the more expensive price per pound
However, what really matters to the consumer is how much the film costs per foot. Even more important than the cost per foot is the cost per load wrapped. The argument for the newer high performance films is that even though they are expensive to make (cost more per pound) they are much lighter in gauge and therefore lighter in weight. For example, high performance film designed to replace an 80-gauge traditional film might be 20% more expensive to make, but it might require 50% less film to hold the load because it works just as well as the material that is 50% thicker. The end result in this example is that the user saves 30% on film costs by switching to the thinner high-performance film.
To precisely analyze price savings, wrap two loads. Then cut the film off of both loads and weigh it on a small sensitive scale. This will indicate the amount of film used for each load. Then multiply the weight of the film by the price per pound (ask your sales person for the weight of the roll or the weight of the case if it is not clearly marked) and divide by the roll or case price. This will yield the price per load. Multiply the price per load by the number of loads typical for each day, each week and so on.
Because there are so many variables with film, users must be very cautious to understand and confirm the math themselves and not to rely on the salesperson's math. Part of the process should always be to adequately sample the new material before accepting any change. The bottom line is that the new material must contain the load as safely and effectively as the old material. Following are four additional considerations for choosing stretch film.
1. Standard or High Performance
This is by far the most important decision. Much of the decision will be based on price, but it needs to be tempered by the requirements of the job. Not that long ago, before the advent of highly innovative stretch films, gauge (thickness) was just about the only thing that mattered. Now it is just one of many considerations.
Standard/true-gauged stretch film offers a great amount of stretch, tear resistance, and strength. The main drawback is waste, because it's not possible for the average worker to apply enough force to reach the maximum stretch potential of the film.
Economy/micron stretch film is a step down from true-gauged stretch film and often comes in a 57, 60, or 63 gauge. The main difference is the thickness and the amount of stretch potential. It is often stiffer and will not stretch as much as a true-gauged film. On the other hand, it is strong, more affordable, and can produce less waste.
Hybrid/multilayer stretch film is commonly used in place of lighter gauge film. It is manufactured in 47, 51, and 53 gauges. It has more layers, is stiffer and has less tear resistance than micron stretch film. Benefits include: lower cost, lighter rolls, and the need for less physical force during application.
The latest and greatest lighter-gauged (less expensive) high performance films are ideal for light to moderate, regular-shaped loads that won't encounter challenging transit or storage conditions. High performance stretch film offers excellent load retention, highly elastic film recovery, high-strength formulation and reduced film neck-down. In the high performance category, even light film gauges have elevated tear and puncture resistance, and excellent cling properties.
But where any or a combination of those conditions are present, heavier (more expensive) traditional films will be the better option and will save money in the long run (less risk of worker injury and damage to loads). Traditional films are considered foolproof and often result in fewer complaints from the warehouse. The precision with which they are applied is not as critical because the weight of the film may help offset a poor application by the worker.
Carefully consider the type of load and even the skill level of warehouse staff. Generally speaking, in a well-controlled environment with nicely cubed loads, the less expensive high-performance films will save money.
2. Hand Film or Machine Film
Hand-held dispensers can be as inexpensive as a few dollars while fully-automatic wrappers run well into the 1,000s of dollars. The general rule is that if the consumer is wrapping 15 or more loads per day, it's more cost-effective to use a machine than to wrap by hand. At that level machines justify their costs by reducing manual labor expense and the possibility of injuries. In addition to the productivity and liability issues, most machines pull the stretch wrap at least 200% before applying it to the load. This results in legitimate savings of up to 50% of film costs. A company that historically used a full pallet of hand film each month might reduce their usage to 6 pallets per year. This savings on film can pay for the equipment very quickly. Also, a machine-wrapped load is generally more secure than a hand-wrapped load. When stretch film is applied by machine:
• Production rates increase
• Labor costs decrease
• Injuries decrease
• Wrapping is consistent
• There is better quality control
• Considerably less film is used because film is stretched properly
So for companies that handle 15 or more loads per day, a stretch wrap machine will more than pay for itself. Following is a summary of hand and machine options.
Manual/Hand Wrappers
• Extended Core: An extension of the film's core creates a natural handle for wrapping. It's an especially economical option since it doesn't require any equipment. The downside is that it provides little control over stretch and is hard on workers' hands.
• Mechanical Brake/Pole Wrapper: A rigid structure supports the film core while a mechanical brake system provides the resistance needed to stretch the film. A pole wrapper is similar, except that the roll sits at the end of an extended pole. This reduces the need for workers to bend and reach during application.
Semi-Automatic Wrappers
• Turntable Wrappers: The load rests on a turntable that spins the load. The film roll automatically moves up and down as it applies the wrap. Stretch is controlled by the speed of the load's rotation and/or the attached pre-stretch feature.
• Orbital Wrappers: The film rests in a carriage housed on a vertical ring. The load feeds horizontally (or vertically in the case of a horizontal ring system) through the center of the rotating ring as the film is applied.
• Rotary Arm Wrappers: The load remains stationary as a rotating arm revolves around it, wrapping the load. These types of wrappers are best for lightweight loads or those requiring high rotation speeds which could otherwise cause the load to destabilize.
Automatic Wrappers
Automatic wrappers are similar to semi-automatic wrappers except that they include a conveyor system for automatic loading. The equipment also applies, seals, and cuts the film.
3. Blown Film or Cast Film
There are two basic methods of manufacturing stretch film---blown and cast. The manufacturing process determines the film properties.
Blown film is manufactured using the blown film extrusion process. The resin is melted, blown out in a giant bubble and air-cooled. This is a slower (more costly) process but results in higher quality. Characteristics are: superior strength, stretch, film memory, and puncture resistance; but poor clarity and very noisy during unwind. It has the superior strength to accommodate irregular loads.
Cast film is manufactured using the cast extrusion process. Instead of being air-cooled, the film is passed over cooling rollers. This makes the cooling process quicker and the product less expensive, but also inferior to blown in important regards, including strength and stretch. Typical characteristics of cast stretch films are: clarity, high gloss, quiet unwind, consistent cling and consistent film thickness. Following is a summary of differences between blown and cast stretch film:
• Strength: Blown is slightly stronger than cast and less likely to tear on a sharp edge.
• Film Yield: Blown films often top out at 200% stretch capacity because the manufacturing process is less controlled and precise. Some of the newer high performance cast films can be stretched to 300%.
• Film Memory: Blown has better film memory (shrinks back to its original size better after it has been stretched). Cast has less memory (this causes loads to shift).
• Load Retention: Blown holds better and won't stretch after it has been applied. While cast retains loads well, it will stretch after it has been applied to the pallet (this also causes load shifting).
• Puncture Resistance: Blown resists puncturing much better than cast, which will generally tear when over-stressed. Blown is more forgiving around sharp edges.
• Visual Clarity: Blown is not crystal clear. This can make reading and scanning harder, but it helps reduce distracting glare. Cast is clear; making reading and scanning under typical warehouse lighting easy.
• Rewind Noise: Blown tends to be very loud when it's unwound from the roll. Cast makes almost no noise.
• Film Cling: Blown has one-sided cling-this creates higher load retention. Cast has a natural cling on both sides. This can make pallets stick together. However, cast film can be manufactured with one-sided cling.
Because of inferior strength and film memory, cast is best for lighter loads with standard shapes. It also tends to be less expensive than blown-which makes it a good choice for less demanding high production applications.
4. Standard or Pre-Stretched
Pre-stretched film is stretched close to its ultimate breakpoint at the factory and then wound onto rolls. This means the film doesn't require nearly as much physical energy to apply as standard stretch film. This is the main reason that pre-stretched films are popular for hand wrapping. In fact, pre-stretched film applied by hand can create the same load stability as machine applications. The rolls are also light and easy to handle and can be applied with a walk-forward wrapping technique, which helps prevent slip and fall incidents. Basically, users get the same (or better) load stability with less product, less physical energy, and greater control.
While pre-stretched film is more expensive per foot than traditional film, it requires about half the amount of film, which can create a net cost savings (the film is much lighter and therefore less expensive per pound). Another plus is that pre-stretched film will naturally tighten after application. This unique film memory and its tendency to tighten after application are the most important reasons for pre-stretching film.
Jobs that make the most sense for pre-stretched film are those that require hand application-especially where workers don't have the strength to handle or tighten traditional film and/or where workers are handling irregularly shaped loads. Pre-stretched film should be used for loads no heavier than 1,200 pounds, since it is usually stretched too thin to hold a heavier load. It can be applied either by hand or with automatic machinery. Companies that position themselves as green can make a good case for using pre-stretched film since it requires less product.
Specialty Wrap
In addition to the 4 considerations mentioned above, there are specialty qualities that are very beneficial for some applications:
• Ventilated: Common applications include anything that needs heat and moisture to vent in order to avoid spoilage, such as produce and other food products.
• Colored/Printed: Using stretch film in a variety of colors or that is printed, makes it easier to identify products and spot tampering. It's also great for product coding and dating.
• Bundling Film: This comes in 2", 3", and 5" widths and replaces tape and string. It has the advantage of not leaving sticky residue or string marks. It's best for packaging small items together.
• VCI: Vapor-corrosion-inhibiting stretch film blocks moisture and contaminants, thus preventing rust and corrosion. It's excellent for products that come into contact with water and other rust/corrosion promoting substances-including rain and salt water vapor typical near seaside docks.
• UVI: Users that store loaded pallets outside for any length of time will need an ultraviolet inhibiting film. However, UVI films vary in how long they will provide protection before the UV properties begin to diminish (usually 3-12 months).
By now you should be fairly certain as to what you need, but probably need a little confirmation. Where can you go for unbiased advice? Look for an industrial packaging supplier that's been in the business for many years and has a stake in your satisfaction. A good packaging supplier will Full HD Film want to establish a long-term relationship based on trust, not a quick sale. So call us now for expert advice that will lead to immediate and long-term cost savings.